Wireless Piezoelectric Mechanical Keyboard
Overview
For the capstone project for my bachelor's degree in mechanical engineering, our team was tasked with ideating an innovative product solution, creating multiple prototypes, and submitting a final production-ready design.
After much brainstorming, the team settled on pursuing my idea of a wireless mechanical keyboard that harnesses energy from each keystroke to power the device. Our challenge was to package and create this electro-mechanical system in a way that provides all the functionality and comfort of a normal keyboard but with the added ability to generate extra power. We found that the optimal method of harnessing the energy was by deflecting piezoelectric elements. We achieved this by modifying the already popular Cherry MX key switch to have a plunger point that contacted the piezoelectric elements.
While we could not obtain the optimal piezoelectric pads for our final prototype due to lead times surpassing the duration of the semester, our final prototype did successfully augment the battery by 8% while typing at a conservative speed of 40 words per minute. With the optimal setup, we estimate that could reach 44% longer battery life.
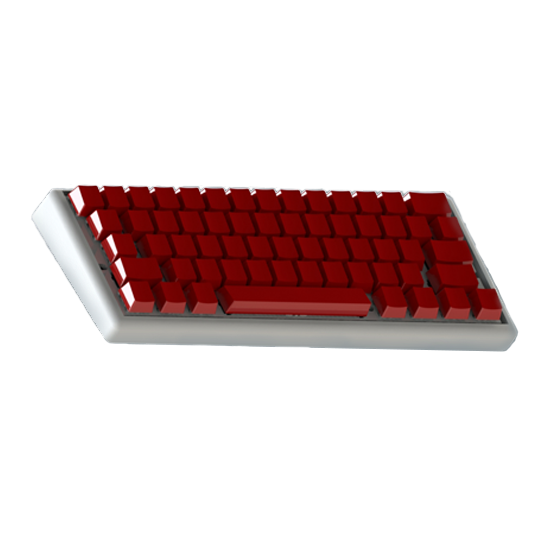
Carnegie Mellon University - Spring 2018
Roles:
Mechanical Engineer: Concept Idea, CAD Models, Prototype Building and Testing, Component Purchasing
Team Members:
Jerrod Coning, Drew Fitzmorris, Sean Graff, David Trzcinski
Concept Designs
There are several ways to convert the mechanical motion of pressing a keyboard switch into electricity, but there are many constraints that need to be considered when designing such as physical space to implement harvesting components, feel when typing, and conforming to industry standards. After considering 4 different approaches, we decided that deflecting a piezoelectric element was the most practical, as it only required the modification of existing switches on the market instead of designing one completely from scratch.
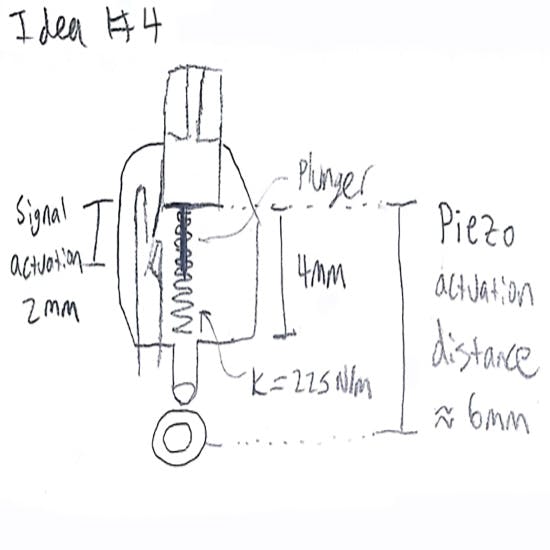
Key Switch Redesign
Our keyboard takes the standard experience with a mechanical keyboard and enhances it by increasing the battery life. As a result, our product needs to maintain the functionality of a mechanical keyboard. Mechanical keyboards offer an improved user experience over their membrane counterparts due to their feel, response time, lifespan, and customizability. Mechanical keyboards operate as follows: when a key is pressed, the plastic slider which is attached to the bottom of the keycap moves down as well. This allows two metal contacts that were previously separated to come into contact with one another. This results in the PCB reading the key as being pressed, and the PCB will transmit this to the computer with a wireless transmitter. When the force of the finger is released from the top of the key, a spring returns the key to the original position, separating the metal contacts and stopping the signal.
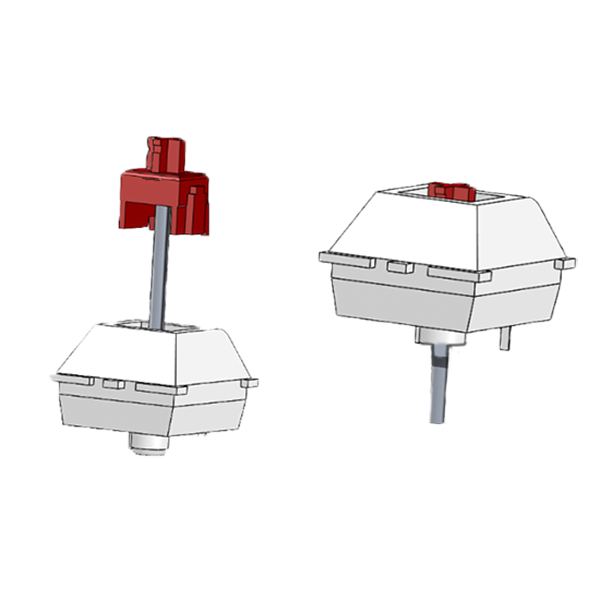
Functional Analysis
Our product will have the same functionality as a standard keyboard with respect to creating and transferring the signal that a key is being pressed. Our additional functionality comes from harvesting the wasted mechanical energy and converting that to usable electrical energy. Instead of the bottom of the plunger hitting a plastic casing and none of the energy being converted, the plunger will now extend out of the bottom of the switch casing and strike a piezoelectric generator underneath. The energy generated from these is then ran through a circuit to make it useable and to prevent the generators from drawing current from the battery when they return to their initial states. This voltage is then stepped to be an appropriate amount that can be cultivated to charge the battery with the battery manager circuit.
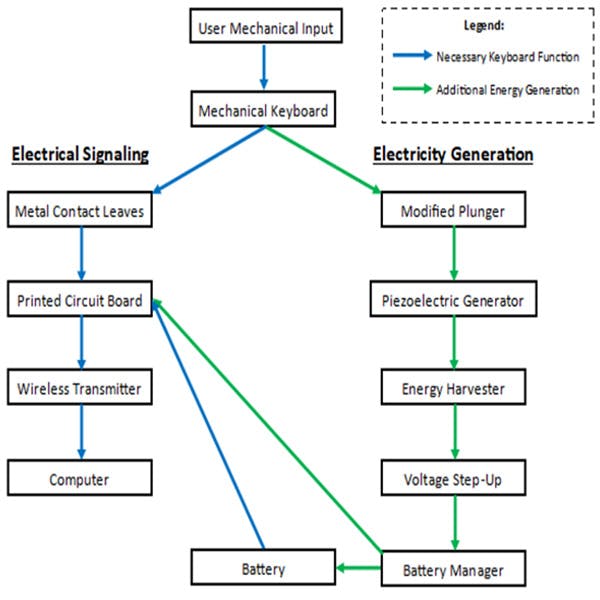
Prototype 1
Our goals for this prototype were to confirm an effective 3D printed plunger can be placed into an existing mechanical switch and still be operational, prove that energy can be harvested using our circuit, prove our circuit can divert the energy and charge the battery, and confirm current “feel” of keys can be maintained with our redesigned switches.
The bottoms of the key switch housings were drilled out so our modified plunger device could strike the piezo pad generators. Instead of doing a full keyboard, we decided to build this prototype in a number pad to reduce build time and cost. A circuit with the energy harvester Arduino was set up to power an LED light to prove that electricity was being converted from the key presses. The prototype was also set up with different spring weights, so we could user test to determine the optimal feel for our new key switch design.
Our prototype produced less output than the theoretical calculations, which could be from the plungers not striking pads ideally and deflecting the piezoelectric element. The keys maintained their feel, and lighting the LED proved that the circuit was harnessing energy.
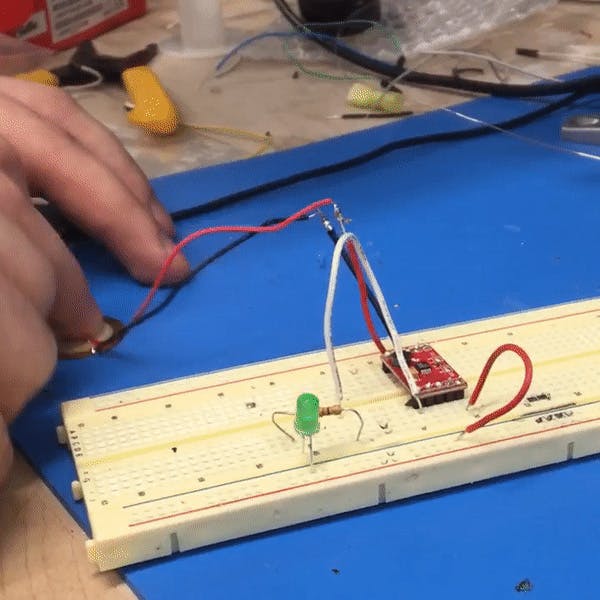
Customer Research
Using the initial prototype, we tested 4 different configurations of our new switch design with varying spring constants. Of the 150g, 80g, and 65g, and 55g springs that were tested, we found that our users like the 80g spring the most. We also asked for feedback regarding the feel of hitting the piezoelectric pads, and users felt it was about equal to “bottoming out” the traditional Cherry MX switch. Using this feedback, we decided to make our second prototype with the 80g springs while keeping the same actuation distance.
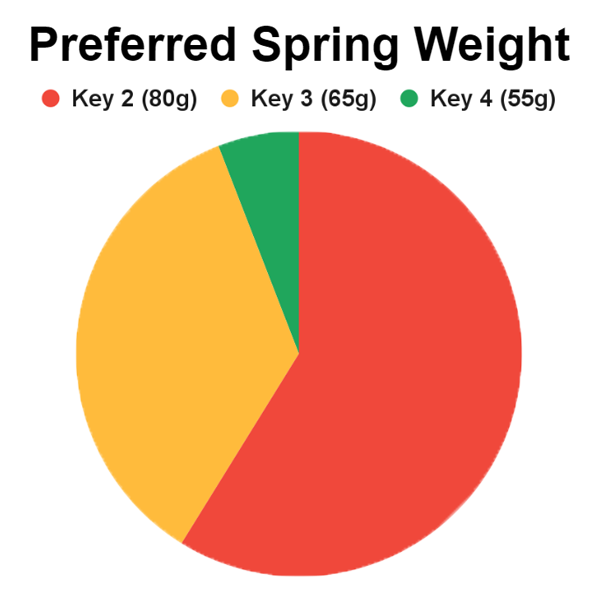
Prototype 2
After we successfully made our first prototype, our goal for the second was to adapt our design for a full keyboard. We also wanted to test encasing the harvesting circuitry as well as test actually charging a LiPo battery.
We chose to make 60% keyboard since the form factor was big enough to prove the concept while saving the budget for our final prototype we would produce for demo day. We aimed to place piezoelectric pads under all keys. To achieve this, the pads were stacked in three layers with varying modified plunger length to achieve the same actuation distance.
Since we did not have access to a 3D printer wide enough to print a full layer of pad holders, we had 6 different prints that joined in the middle of the board. We found that this made the center of the keyboard flex too much internally which disrupted typing and altered the striking point of the plungers on the piezoelectric pads. To fx this, we decided to mill the pad holders out of nylon.
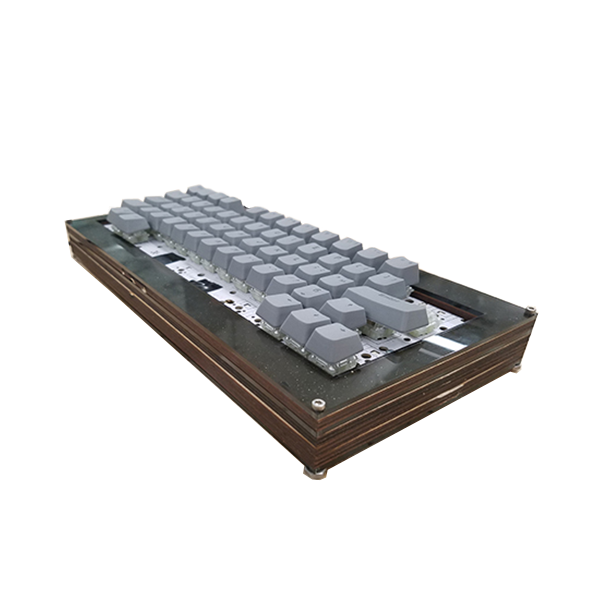
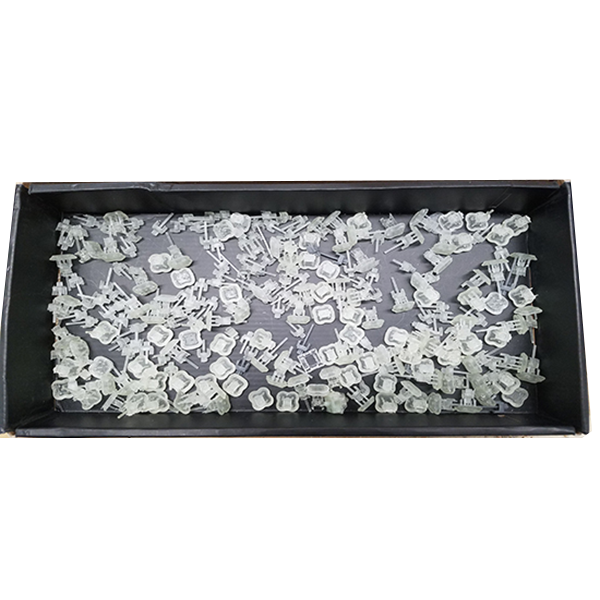
Demo Day Prototype
The prototype successfully extended the battery life by 8% at a typing speed of about 40 words per minute. We had to increase the height and size of casing to accommodate fitting all of the circuitry inside of the device, but we found that we could reduce some thickness and achieve similar energy outputs by placing our switches under 25 of the most frequently used keys. We soldered our switch designs into the PCB of an existing keyboard and we placed the piezoelectric elements into a CNC machined nylon housing.
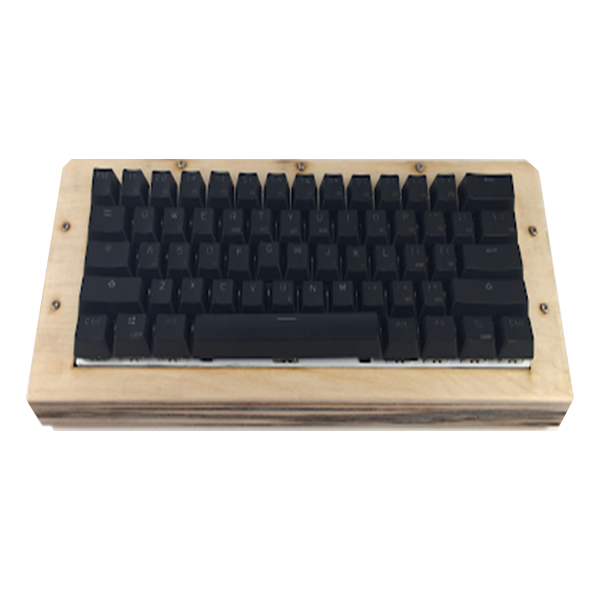
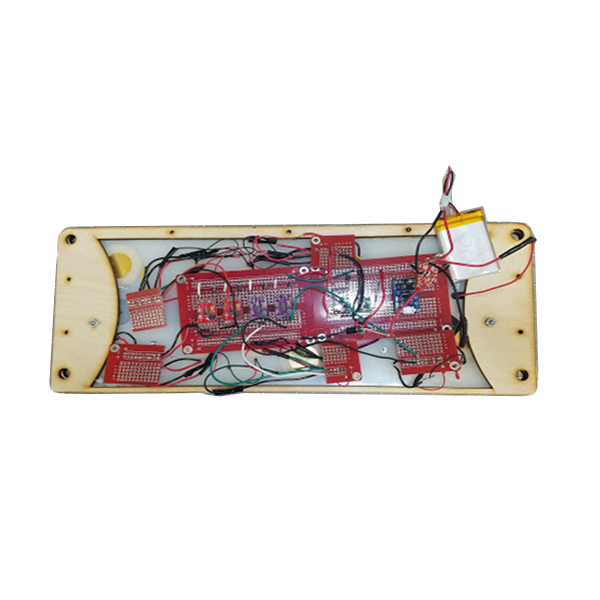
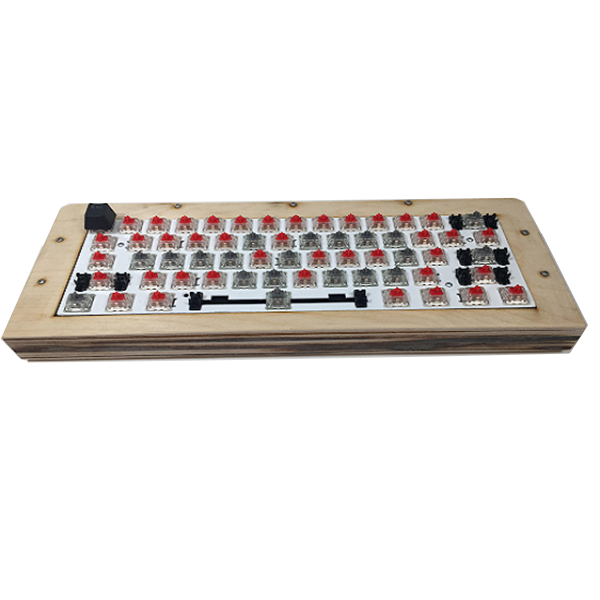
Production Design
The final design for our piezoelectric wireless keyboard meets the design specifications set forth and effectively extends the battery life by 44%. One limitation of this design is the total lifespan of the product which is reduced due to the piezoelectric elements only being reliable for 20 million hits rather than 30 million hits on competitor keyboards. While the keyboard would still be functional, the energy generation would reduce over time. We believe that the added battery life for the majority of the total product life provides enough values to the consumer to be a compelling product. To ensure this product is profitable, we recommend a high amount of R&D to further improve electricity generation from the piezoelectric generators. User feedback showed a high interest in the product if it were to reach near self sustainability.
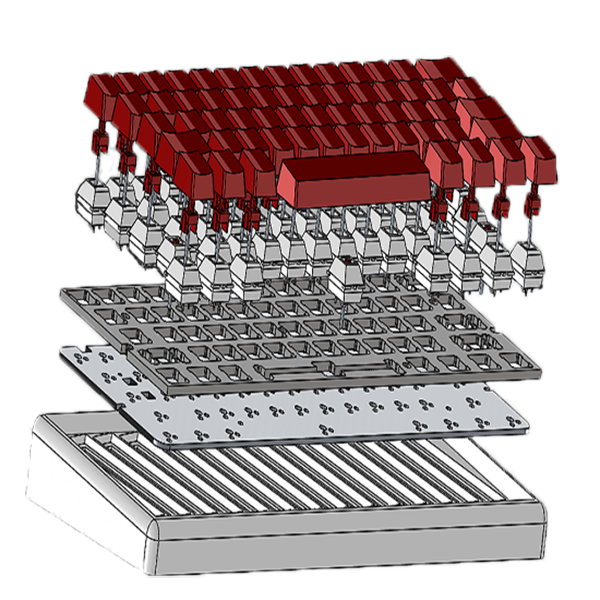
Poster from Demo Day
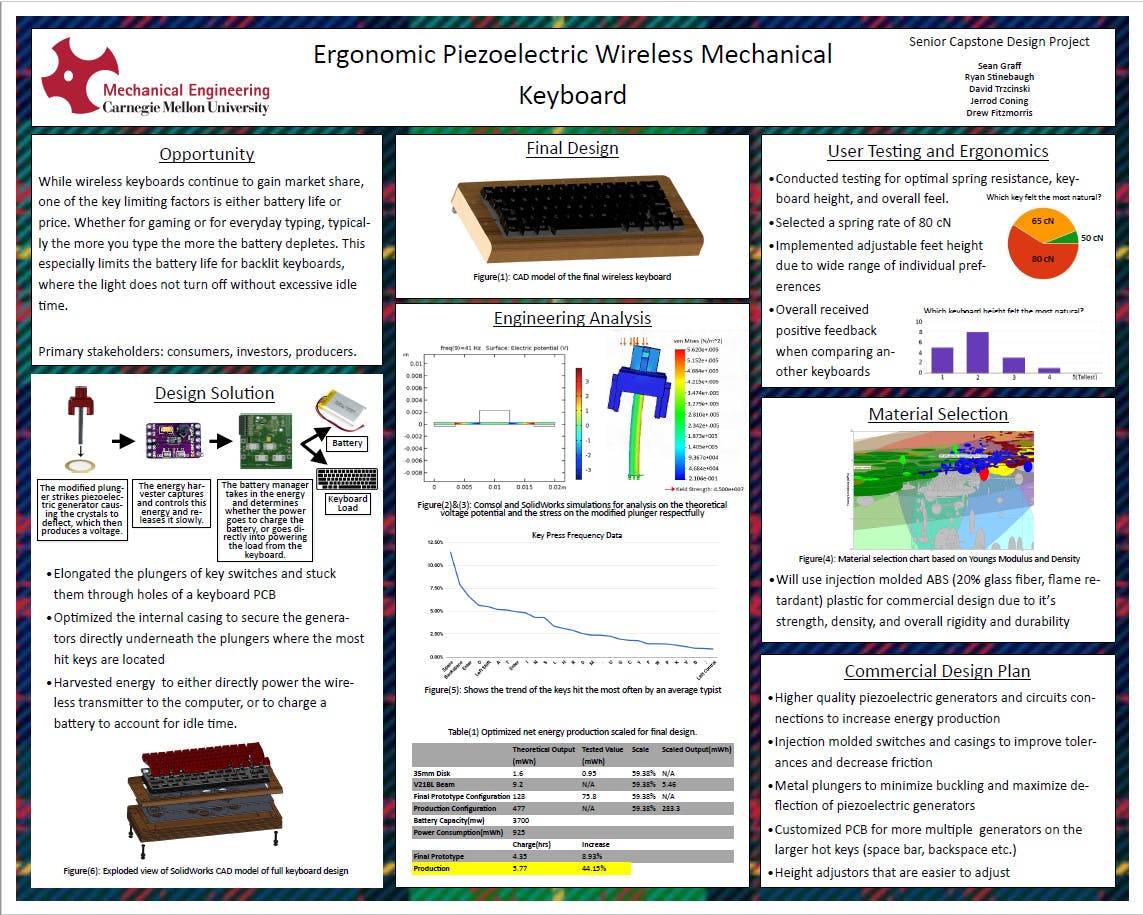